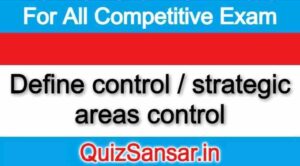
Define control / strategic areas control
Meaning and Definition of Control
Control is a basic managerial function which implies measurement and correction of performance of subordinates to ensure that the predetermined objectives are accomplished. It also involves taking corrective actions in case the performance is not satisfactory.
According to E. F. L. Brech, Control is the process of checking actual performance against the agreed standards or plans with a view to ensuring adequate progress or satisfactory performance.
Strategic Areas of Control
Three kinds of control systems are used by the modern organisations, namely- (i) historical or feedback control, (ii) concurrent control, and (ii) predictive or feed forward control. The details of these controls are discussed below:
1. Feedback Control: Feedback or Post-action control measures result from a completed action. The causes of deviations from the standards are determined and corrective steps are taken so that such deviations do not occur again. In all physical and biological systems, some message is transmitted in the form of mechanical transfer of energy, a chemical reaction, or any other means which is known as ‘cybernetics‘. In social systems also, some information is sent back to exercise control. Any good managerial system controls itself by information feedback which discloses errors in accomplishing goals and initiates corrective action. Feedback is the process of adjusting future action based upon information about past performance. Though feedback is ‘after the fact’, it is still vital to the control process. Sometimes, input variables are unmeasurable (e.g., the values an employee brings to the job) or are not detected at the feedforward control point. Feedback is necessary in any continuous activity as it enables to take corrective action which is essential for the accomplishment of goals of the system.
The concept of feedback is important to the development of an effective control system in any organisation. Managerial control is somewhat akin to the thermostat system of a refrigerator. Thermostat is a control device of closed loop type that makes control instantaneous. In a refrigerator, thermostat records the actual temperature inside the refrigerator, compare it with the required temperature and instantaneously initiates action to bring the actual temperature to what is required. Similarly in an organisation, management needs continuous flow of information about actual performance so that deviations are promptly corrected. Information which the management receives is nothing but feedback. Feedback information may be received formally or informally. Formal feedback involves all written information about actual performance, reports, financial statements, etc. But informal feedback, on the other hand, is through personal observations, personal contacts and informal discussions.
Managerial control can’t be so instantaneous or self-correcting as thermostat system or any other mechanical or electronic system. There always exists a time-lag between recording deviations and taking corrective actions even when sophisticated system of data collection is used. The collected information needs to be analysed properly before suggesting any corrective action.
2. Concurrent Control: It is also known as ‘real time’ or ‘steering’ control. It provides for taking corrective action or making adjustments while programme is still in operation and before any major damage is done. For instance, the navigator of a ship adjusts its movements continuously or the driver of a car adjusts its steering continuously depending upon the direction of destination, obstacles and other factors. In a factory, control chart is an example of concurrent control. Safety check is another illustration in this regard. Concurrently control occurs while an activity is still taking place.
3. Feedforward Control: Feedforward control involves evaluation of inputs and taking corrective measures before a particular sequence of operations is completed. It is based on the timely and accurate information about changes in the environment. If right information is not available in time, feedforward control is likely to be imperfect. Feedforward follows the simple principle that an organisation is not stronger than its weakest link. For instance, if a machine is not functioning properly, the operator will look for certain critical components to see whether they are working well or not. The same logic applies to feedforward control it is essential to determine and monitor the critical inputs into any operating system. Preventive maintenance programme is an important example of feedforward control. It is employed to prevent a breakdown of machinery. Another example of feedforward control is formulation of policies to prevent critical problems from occurring. For instance, a policy on absenteeism may be communicated to new employees to help prevent potential problems due to absenteeism.
Feedforward control may be used with great advantage if the following guidelines are followed:
(i) Thorough planning and analysis must be done.
(ii) Adequate care must be taken in selecting input variables.
(iii) Data on input variables must be regularly collected and assessed.
(iv) The feedforward control system must be kept dynamic.
(v) Corrective action must be taken as suggested by feedforward control.